HUNTSVILLE, Ala. – Army officials are breaking ground on a decades-long environmental remediation project to lift contaminants out of acres of land located on Redstone Arsenal near Huntsville, Alabama.
Across football field-sized areas that became contaminated with industrial chemicals, workers employ a hot new approach to soil and groundwater remediation. They use an environmental treatment method called electrical resistance heating to boil contaminates out of acres of land for reutilization.
Due to missile and rocket manufacturing during World War II, large swaths on the southeastern portion of the arsenal have been contaminated with solvents, such as the chlorinated solvent Trichloroethylene lost in the manufacturing process. This chemical has leached deep into the water table in a widely dispersed plume, or a shape resembling a feather, and is considered a continuing source of contamination to the groundwater by the Alabama Department of Environmental Management. Today, the Garrison Installation Restoration Branch in partnership with the Savannah District U.S. Army Corps of Engineers, lead efforts to remediate vestiges of the post’s past.
Starting in the mid-1990s, the Army investigated 900 Redstone sites for possible treatment and identified 385 for further investigation. ERH sites selected for treatment occupy land that could be redeveloped, but groundwater and soils fall below regulatory standards. Army officials selected ERH, a value-based, preferred method of cleanup for these highly-contaminated sites that proves capable of achieving the arsenal’s redevelopment goals. The Army contracted investigation and remediation work to the Chicago Bridge and Iron Company, which subcontracted specialty work to Technology Development for Thermal Remediation Services (TRS), according to Barry Hodges, a U.S. Army Corps of Engineers, Savannah District scientific and technical lead.
“As with most military installations, many of the most heavily contaminated areas are also in those areas that the arsenal would most like to reutilize, as these are the best geographical areas of the arsenal,” said Hodges.
ERH remediation costs are site specific and dependent on the shape and volume of the treatment area, target contaminants and level of contaminant reduction required, said Greg Beyke, vice president of TRS.
Compared to other methods of removal such as “pump and treat,” which extracts contaminated groundwater through recovery wells or trenches and treat groundwater above ground, ERH can clean sites where other methods have had limited success.
For a typical commercial site requiring a 99 percent reduction of TCE in soil and groundwater, the total price for ERH remediation is currently about $400,000 plus $60-100 per cubic yard of treatment. ERH outpaces alternative methods in effectiveness and adaptability, and is currently the only remediation treatment that can be performed with guaranteed results. While “pumps and treat” methods cost less, ERH cuts decades worth of treatment time by cleaning sites within 6-12 months compared to 20-40 years of “pump and treat” methods, said Hodges.
The ERH process
ERH is a robust remediation technology that can quickly reduce masses of volatile organic compounds in soil and groundwater. ERH evenly heats the subsurface to the boiling point of water by passing electrical currents through contaminated soil, rock, and groundwater. Soil, a defiant conductor of electricity, resists electrical flow. This resistance causes gentle heating which evaporates volatile contaminants in place and steam strips them from the subsurface. Vapor and steam are then extracted, cooled, and treated using standard methods. About 150 ERH remediation projects have been completed in the U.S. to date, said Beyke.
Deploying ERH requires a power control unit to control the application of power, electrodes to deliver power to the subsurface, recovery wells to collect steam and contaminant vapors, a steam condenser, a vapor treatment system, and control and data acquisition systems, said Beyke.
The technology works in all soil types and can be applied under operating facilities and public areas. ERH is also frequently used to remediate sedimentary rock. However, due to Redstone’s complicated geology, a goal of 80 percent reduction was negotiated with the state of Alabama, said Hodges.
“There is a cost-benefit calculation that one must keep in mind towards the end of the effort,” said Hodges. “As you approach ‘clean’ it gets harder and harder to remove the contaminant. At some point you cross the point that the benefit no longer justifies the cost. It’s critical that the designers choose a goal that is achievable before one enters the ‘this is no longer making sense’ range."
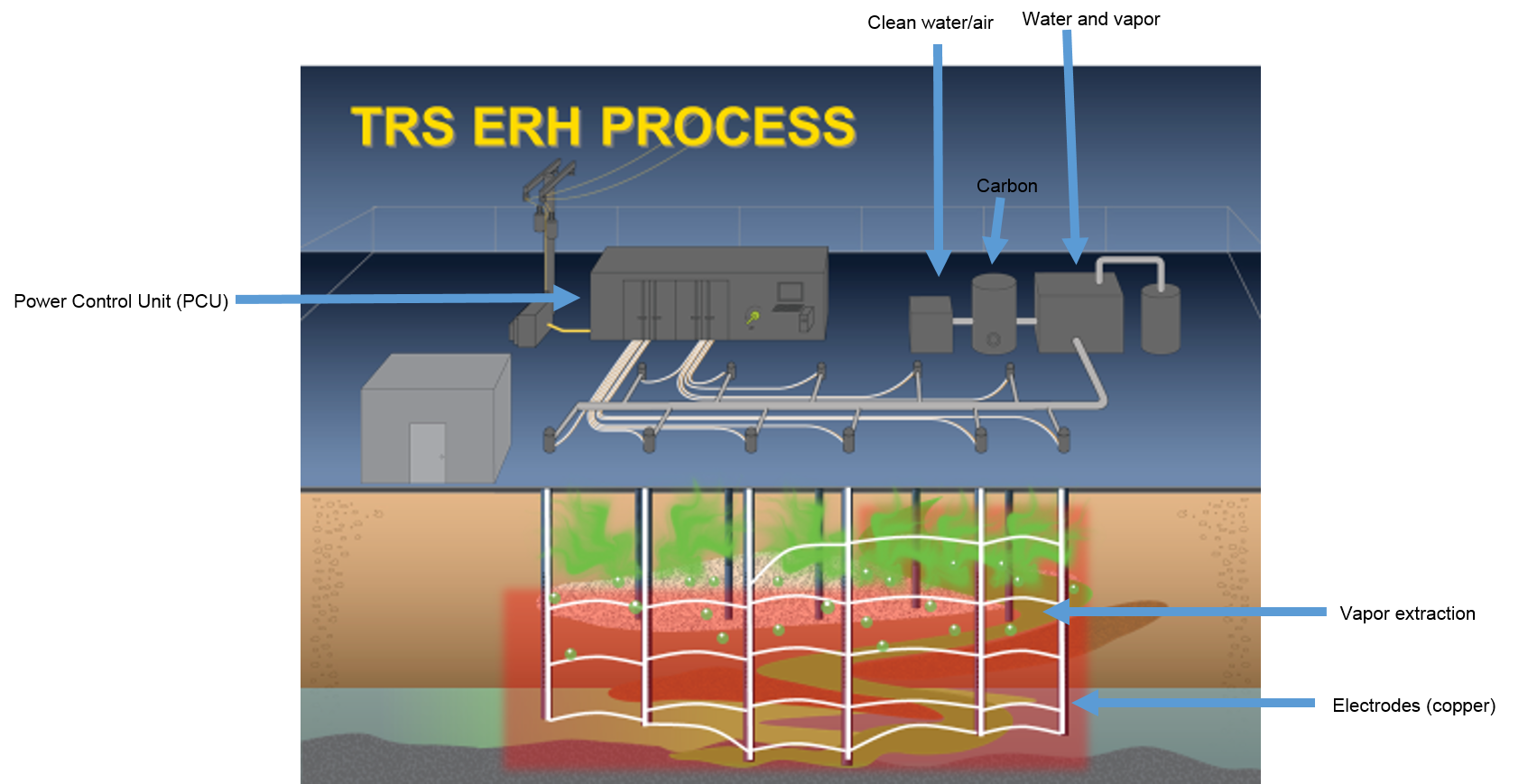
Understanding the geology
Before selecting an optimal remediation method, the Army conducted studies to understand the complex geology of the area. Across Redstone’s more than 38,000 acres and what Hodges describes as “bipolar geology,” they found that about 20-50 feet of its geology are remnants of limestone bedrock that slowly broke down over time to produce red clay. The remaining geology is a type of limestone called karst rock.
“Think of a box full of [cooked] spaghetti but generally trending in one direction,” he said. “That is what karst looks like. Finding the voids are hit or miss.”
While water moves slowly through overlying red clay, groundwater penetrating deep into karst networks moves extremely fast, said Hodges.
“This impacts the effectiveness of the ERH system,” said Hodges. “This means that new cold water is constantly being introduced into the system and more energy is required to maintain [boiling] temperatures.”
Looking ahead
For nearly a decade, the Environmental Management Division has successfully treated five contaminated sites at Redstone, including difficult karst limestone environments found on land at the post.
“It’s been a huge success for us,” Hodges said.
To date, roughly 20 sites remain. Though cleanup work will continue for years, the vast majority of investigation work is complete.
“In about eight years, we have essentially defined Redstone’s universe,” Hodges said. “Redstone will be spending many decades finishing the cleanup work but we are beginning to make real progress.”